The initiative, funded by the IC4D Trust Fund at the World Bank and launched last September, aimed to assess the feasibility and the market opportunity to turn PET plastic waste into 3D printer filament that can be sold locally or globally, and to then print unique and local marketable products, which could be then traded and sold by waste collectors back to their communities. It also aims to build local capacity on making and digital fabrication in countries like Tanzania. More background on the initiative can be found here.
Additive manufacturing is one of the most widely accepted emerging technology and its services are being used by various industries, including medical, automotive, consumer products, military, academia and others. Alongside the usage of 3D printers in various industries, entry level printers which produce products of relatively smaller volumes are also currently available and mainly purchased by hobbyists, educational institutes and design firms.
As traditional printers need ink cartridges in order to print, 3D printers need plastic filament. Most of the filament produced today is from virgin, unused petroleum-based plastic which generates not only increasing amounts of global waste but contributes to carbon emissions, resulting in significant environmental damage. This provides a unique recycling opportunity to make filament out of used, plastic waste, specifically from PET plastic, which is the basis of soda bottles, consumed by many people around the world.
As part of the ReFabDar initiative, Tech4Trade, STIClab, and other partners developed a low-cost, custom-extruder to produce filament from recycled PET plastic. Based on the principles of open collaboration and standards, the designs of the extruder are available on an open source license at Wevolver. This now opens up new market opportunities for emerging economies for local filament production and at a lower cost.
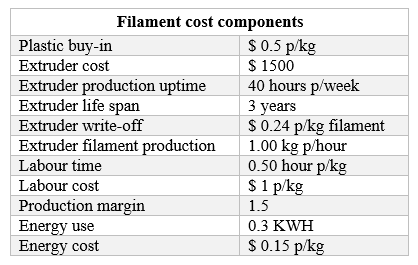
low-cost extruder
The filament can be sold to businesses (60% of the market) and individual consumers (40%).
Business-to- business opportunities include:
- Tech Universities and/or private high schools;
- 3D Hubs (both local and worldwide) – there are over 25,000 maker spaces and print labs worldwide;
- FabLabs (small scale workshop offering digital fabrication equipment and activities)
- Local entrepreneurs looking to set up businesses in 3D printing;
- Companies selling 3D printers but who do not produce their own filament.
- 3D print enthusiasts;
- Hobby printers and home owners.
Opportunities:
- The 3D printing market is booming: it was globally valued at US$2.5 billion in 2013, and is estimated to grow to a staggering $16.2 billion market by 2018. Similarly, the market for polymers used in 3D printing for the production of filament reached $310 million in 2014 and is estimated to grow to $1.4 billion by 2019.
- Currently the largest 3D printer markets are the USA, Germany, Netherlands and China. The Middle East and African markets are also expanding rapidly. The domestic East African market is still limited due to lack of knowledge, infrastructure and clear use cases, but has a high potential for growth.
- Based on some basic assumptions, the cost of producing a spool of filament amounts to approximately $2.84 p/kg. Globally, a spool of filament is priced between $19-$175p/kg depending on material, diameter (mm), color or other specific characteristics. In Tanzania, a spool of filament can cost up to $60-$80, including shipping costs from China.
- Among the main challenges of the production of recycled PET filament is complexity of the distribution, particularly since shipping costs to many locations risk being very high.
- Ensuring an ongoing, clean and high quality supply of plastic is also a significant challenge to producing recycled PET filament. This can be done either by working directly with waste pickers or through a third party (i.e. a local recycler who in turn works with waste pickers).
- Creating a social brand in a market which is currently unbranded, and increasing the popularity of PET filament as opposed to more widely used plastics. On the other hand, there are significant opportunities in producing recycled PET filament.
- Perfect the extruder design so that it is ready to produce consumer-ready filament;
- Create a local network of plastic collectors that can supply high quality PET plastic on a continuous basis;
- Establish a formal production site, ideally close to collection point, that can consistently produce small amounts of filament for the local market;
- Set up the impact framework for redistribution of profits back to waste pickers;
Join the Conversation